Power and Free Conveyors by Webb-Stiles
Power & Free overhead conveyors are built for flexibility, control, and complex routing. These dual-track systems let loads stop, start, accumulate, and divert independently—ideal for high-throughput assembly lines, robotic integration, and sequencing workflows.
Unlike monorail systems, Power & Free conveyors allow variable pacing and automated switching. They can move multiple carriers at once without disrupting downstream operations or line balance.
Webb-Stiles engineers Power & Free solutions in-house, including the manufacture and rebuild of all trolley assemblies at our Gadsden, Alabama facility. This in-house process improves lead time, ensures consistent quality, and provides long-term system support.
What makes Power & Free Unique?
Independent Carrier Control
Power & Free conveyors use a dual-track system — a powered chain on one track and free-trolley carriers on another — to allow multiple loads to move independently through a shared line. This design makes it possible to stop, accumulate, or divert specific carriers without affecting others. It’s ideal for high-mix or variable-speed environments.
Smart Routing with Switches and Stops
Systems can be configured with merge points, diverters, and stop stations to support load sequencing, indexing, or zone-based workflows. From robotic cells to manual workstations, Power & Free allows flexible routing that keeps production flowing — even when individual carriers pause or hold for processing.
Built for Complexity, Not Compromise
These systems thrive in applications where simple conveyors fall short: buffer zones, asynchronous movement, in-line inspection, or controlled interaction with automation. They allow precise control at every point along the track, making Power & Free ideal for paint lines, assembly operations, and high-throughput production cells.
Over & Under vs. Legacy Side-Push Systems
Over & Under Power and Free
The traditional configuration.
The powered chain rides above the free trolley track. This allows trolleys to move smoothly below and disengage at accumulation or stop zones. The layout supports tighter turns and elevation changes while keeping the power line accessible from above.
Why it works:
This vertical arrangement is ideal when floor-level space is limited and you need uninterrupted movement beneath utility lines.
Best for:
High-density layouts, vertical movement, and multi-level facilities.
Side-Push Power and Free
An alternative layout for tight clearances.
Side-Push systems use a powered chain that runs parallel to the free trolley on the same level. A lateral push dog engages the trolley from the side, delivering full Power & Free functionality with a flatter system profile—ideal when vertical space is limited.
Although Side-Push systems are specified less frequently today, Webb-Stiles continues to offer Side-Push configurations for applications where their layout provides distinct advantages. We also support, refurbish, and modernize existing Side-Push installations to ensure long-term reliability.
Best for:
Low-ceiling applications, mezzanine installs, or environments where top-access isn’t practical.
Understanding Power & Free Trolleys
Over & Under Trolleys
Our Over & Under Power & Free systems use a combination of leading, intermediate, and trailing trolleys that run inside dual steel channels mounted toe-to-toe and connected by steel plate yokes. These trolleys disengage from the power chain to allow stopping, switching, or accumulation across powered and non-powered paths.
-
Front Accumulating Trolley (Leading): Drives the carrier assembly using a retractable dog that engages with the power chain.
-
Intermediate Trolleys: Help distribute weight on heavy carriers or provide articulation for long or bulky loads, especially through curves and inclines.
-
Rear Trolley (Trailing): Features a beaver tail that actuates the front trolley’s paddle for automatic disengagement during accumulation. Optional push-thru dogs can be used to transfer loads along the free track.
We manufacture both casted and bolt-together styles. Our current standard is a 3″ bolt-together design for cost-effective, precision assembly. New 4″ and 6″ versions are currently in development.
Side-Push Configurations
In Side-Push systems, trolleys travel along a single I-beam. Carriers—either accumulating or not—connect with a pusher bar and engage with a powered chain dog that moves the load from the side. This horizontal engagement method offers a flatter system profile, well-suited for specific applications with tight vertical constraints.
Webb-Stiles continues to engineer new Side-Push systems when project requirements call for it, while also providing comprehensive support for refurbishment and modernization of existing installations.

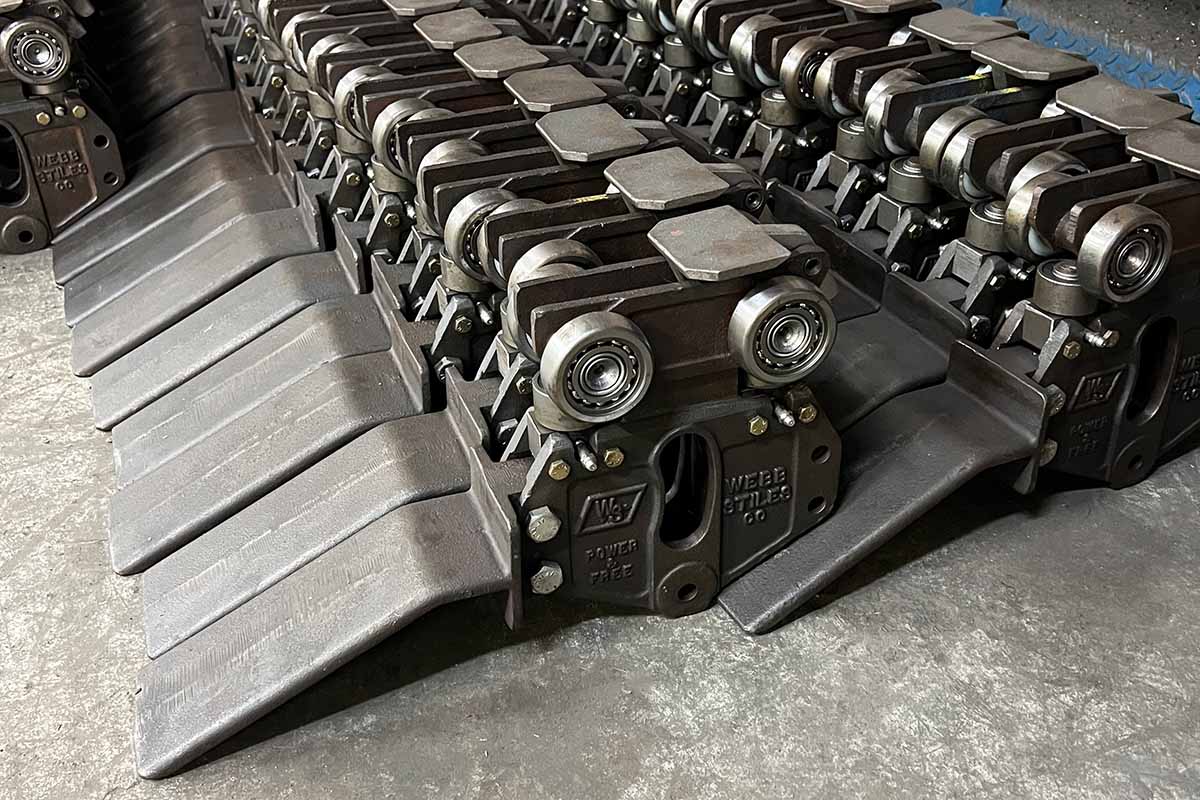
Power & Free System Features
System Functionality
- Dual-track layout enables independent control of each carrier
- Carriers can stop or accumulate at any point in the system
- Merge, divert, or exit using precision-configured switches
- Pneumatic or manual stops to match application needs
- Push-thru dogs and chain disengagement mechanisms for smooth accumulation
Mechanical Design
- Offered in 3″, 4″, and 6″ track sizes
- Compatible with Over & Under or Side-Push configurations
- Drive options include caterpillar or sprocket units
- Screw-type, spring-loaded, or air-operated take-up systems
- Guide wheels and carrier spacing are engineered per load
- Optimized for indexing, sequencing, and robotic integration
Downloads & Literature
Get detailed system specifications and layout planning info for Power & Free conveyors.
Have a complex layout or system in need of control?
Contact our team to discuss your Power & Free application, whether you’re planning new automation or troubleshooting an existing line.