Vertical Conveyors by Webb-Stiles
What are Vertical Conveyors?
Vertical conveyors move materials between elevations—either lifting or lowering loads from one level to another. As a result, they support tighter footprints, faster throughput, and more controlled transitions between production zones, mezzanines, docks, or storage levels.
Webb-Stiles offers several types of vertical conveyors for different applications. For example, continuous-speed lifts support high-volume packaging lines, while servo-controlled platforms deliver precise positioning for heavy assemblies. Many facilities integrate these systems into distribution centers, manufacturing plants, and shipping or receiving areas.
In many cases, Webb-Stiles designs vertical conveyors to be self-supporting, eliminating the need for structural tie-ins. Units may be front-loading, side-transferring, stationary, or portable—and they use hydraulic, pneumatic, electric, or servo-powered drives. Ultimately, each system is custom engineered to match the layout, product, and performance of the job.
Types of Vertical Conveyors
Continuous Vertical Conveyors (CVC)
Continuous vertical conveyors—often called Speed-Lifts—move products in a nonstop loop using a rotating platform system. As one load rises, another descends, creating a steady, uninterrupted flow. As a result, these systems support high-volume environments where timing and consistency are critical.
Best for: High-speed, high-throughput systems like packaging lines, sortation zones, or redistribution centers.
Scissor Lift
Scissor lifts raise product using a pantograph-style structure powered by hydraulics or electric motors. The platform travels straight up and down without rotating, which simplifies the motion. In many cases, these lifts are used to vertically position pallets, equipment, or conveyors in limited space.
Best for: Floor-level elevation changes, workstation lifts, or applications where compact vertical motion is required.
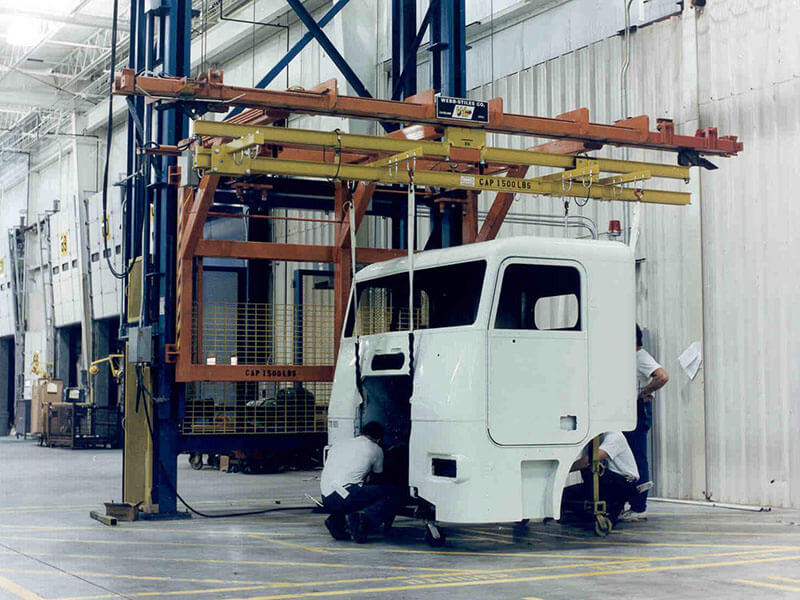
Vertical Reciprocating Conveyor (VRC)
A vertical reciprocating conveyor lifts and lowers a platform between levels in a stop-and-go cycle. Unlike continuous systems, a VRC pauses at each level to load and unload. As a result, this makes it ideal when flexibility is needed for large items, variable loads, or multi-height transfers.
Best for: Forklift interfacing, mezzanine access, or facilities with changing load types and vertical stops.
Screw Jack Lift
Screw jack lifts rely on multiple synchronized jacks to raise a platform with consistent precision. Because of this, these systems perform best when the platform must stay level across all corners—even under uneven or shifting loads.
Best for: Engine assembly, fixture positioning, or conveyor platforms that demand exact vertical control.
Applications & Uses
Webb-Stiles vertical conveyors help move product safely and efficiently across docks, floors, and facility levels. As a result, they’re used in everything from engine assembly to overseas air freight operations.
Manufacturing & Assembly
-
Webb-Stiles lifts engine blocks up to 100 feet for overhead accumulation
-
Facilities use lifts to move torque converters between production zones
-
Live roller conveyors can be mounted on platforms for easy workstation access
-
Screw jack lifts raise fixtures or conveyor sections with precise control
Shipping & Receiving
-
Vertical lifts transfer product between dock and warehouse storage
-
High-speed units lower finished goods directly to outbound lines
-
Reversible lifts enable two-way transfer across loading bay zones
-
In many cases, lifts automatically stage or unload from carton down-stackers
Warehousing & Multi-Level Facilities
-
Moves totes, pallets, and parts between upper/lower floors
-
Enables high-volume material flow on compact footprints
-
Replaces standard freight elevators with higher cycle rates and no operator requirement
-
Self-supporting systems used for temporary or mobile warehouse installations
Aerospace & International Logistics
-
Webb-Stiles tests platform lifts for air freight before deployment
-
Webb-Stiles installs reciprocating lifts with integrated catwalks to feed overhead conveyors.
-
Installed systems include overseas applications
Key Features
Webb-Stiles engineers vertical conveyors for performance, flexibility, and precise control—custom built to match your facility, flow, and load.
Engineered for Load, Layout, and Performance
-
Webb-Stiles lifts handle cartons, engine blocks, and everything in between—up to 1,000+ lbs
-
In addition, these systems can run at speeds up to 120 ft/min
-
Reversible platforms allow bidirectional product flow
-
Load configurations include front-loading, side discharge, or pass-through layouts
-
Screw jack lifts deliver precise, level movement
-
In many cases, portable self-supporting frames reduce structural tie-in costs
-
These systems integrate easily with conveyors, fork trucks, or standalone workstations
Designed, Built, and Controlled In-House
-
Webb-Stiles builds every system to spec—no off-the-shelf retrofits
-
Integrated controls use electronic, hydraulic, pneumatic, or PLC-based logic
-
Platforms include live rollers, turntables, bolsters, or part-specific fixtures
-
Webb-Stiles tests all systems in-house, including those deployed internationally.
-
As a full-service partner, Webb-Stiles manages layout, fabrication, and control integration
How Vertical Conveyor Systems are Engineered
Every vertical conveyor system starts with one goal: moving product between levels without disrupting what’s happening around it. Whether you’re feeding a mezzanine, bypassing an aisle, or lifting to overhead storage, the design depends on the layout, the load, and the flow of work.
Product & Platform Requirements
Webb-Stiles begins by evaluating the product’s size, shape, and weight. Whether you’re moving pallets, racks, cartons, or castings, we determine the right lift capacity, platform style, speed, and cycle timing to match the flow of your process.
System Layout & Transfer Method
The physical layout drives how each lift is configured. We plan for front or side loading, inline or 90-degree discharge, and whether the lift will transfer to a conveyor, a workstation, or a forklift zone. Your overall system layout dictates the handoff—and we design the lift around it.
Drive Style & Motion Control
Webb-Stiles powers each vertical system using screw jacks, hydraulic cylinders, air lifts, or servo motors—each selected to balance speed, control, and duty cycle. We match the drive system to your layout and product flow, whether you’re running continuously or in timed cycles.
Controls, Safety & Integration
Webb-Stiles builds all control systems in-house. Depending on your application, we may integrate sensors, timers, PLC logic, or operator stations. Ultimately, Webb-Stiles builds safety features like guarded lifts, skirts, and controlled stops to match your environment and standards.
Downloads & Literature
Looking for technical specs or layout examples? The brochure below includes a full overview of vertical conveyor types and Webb-Stiles’ engineered capabilities.
Ready to move your product up?
Contact our team to start a conversation.