Overhead Conveyors by Webb-Stiles
What is an Overhead Conveyor?
An overhead conveyor is a material handling system that moves products along a suspended track, allowing items to travel above ground-level operations. These systems use trolleys mounted to an I-beam or enclosed track to transport parts through workstations, paint booths, ovens, or storage areas—without interrupting activity below. Often referred to as monorail systems, especially in the case of traditional I-beam designs, overhead conveyors are especially useful in facilities where floor space is limited or where equipment needs to move across complex production zones. Compared to floor-mounted systems, they free up valuable real estate and reduce the risk of ground-level congestion or collision.
Overhead systems can be configured for continuous or stop-and-go movement and may include features such as elevation changes, curves, or switches. Many facilities integrate these systems into assembly lines, finishing systems, and high-density storage layouts to support efficient product movement through multiple manufacturing stages.
History of the Overhead Conveyor
The overhead conveyor has its roots in late 19th-century innovations that transformed material handling and manufacturing. Early developments came from pioneers like Andrew Betts Brown, who in 1863 invented the overhead travelling crane used in building London’s Blackfriars Bridge. This concept evolved further in 1876, when Sampson Moore designed the first electric overhead crane for hoisting heavy loads at the Royal Arsenal in Woolwich. By 1892, John Ridley Temperley introduced the Temperley transporter, an early version of the overhead crane that moved materials more efficiently and laid the groundwork for the systems we recognize today.
While these early inventions focused on lifting and moving heavy items, they set the stage for continuous movement systems that would soon become essential in manufacturing. The overhead conveyor, as a production tool, gained widespread attention in the early 20th century when Henry Ford integrated it into his automotive assembly lines. Although Ford did not invent the overhead conveyor, his pioneering use of it to streamline vehicle production revolutionized manufacturing and made the technology a staple in factories worldwide.
Since then, overhead conveyors have continued to evolve, becoming vital for industries that require efficient, space-saving material handling solutions. Their ability to improve workflow, maximize floor space, and adapt to a variety of applications ensures their relevance in modern manufacturing environments.
Types of Overhead Conveyors
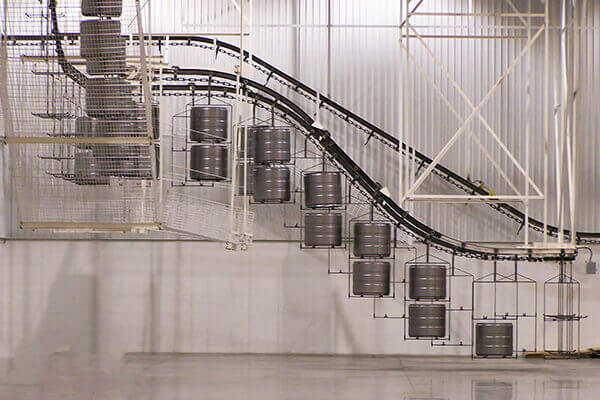
Monorail Conveyors
Monorail Conveyors are a type of overhead system where carriers move along a single, fixed path powered by a chain. Each trolley attaches directly to the chain and travels the same route at a constant pace. This setup makes monorail systems ideal for linear, uninterrupted movement. These conveyors are commonly used in paint lines, curing ovens, and workstations where repetitive motion is required.
Because monorail conveyors follow a set path without diverging or stopping independently, they are best suited for applications that prioritize simplicity and reliability over routing flexibility. Their streamlined design reduces floor-level traffic and supports predictable product flow in controlled environments.
Best for: Streamlined processes, repetitive movement, and controlled layouts.
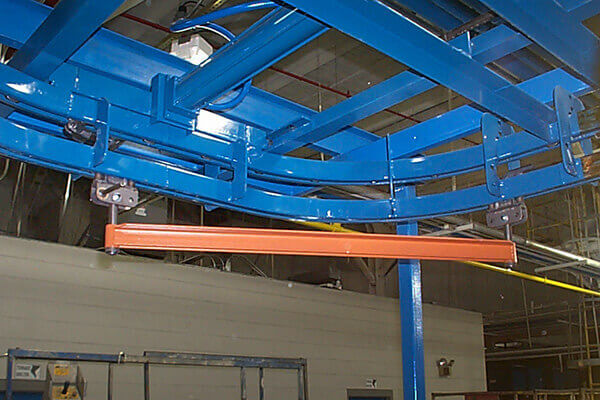
Enclosed Track Conveyors
Enclosed track systems use a compact tubular steel rail to fully enclose the chain. This helps minimize contamination while delivering smoother, quieter performance. The enclosed design protects internal components from debris and damage, making it ideal for clean or controlled environments.
These systems are a smart choice for facilities with space constraints, tight routing paths, or process zones that require reduced noise or airborne particulates. Their low-profile design also supports tight curves and elevation changes without compromising functionality.
Best for: Clean environments, tight layouts, lighter to medium loads, and quiet or sensitive production areas.
Note: Enclosed track is often used as a monorail variant.
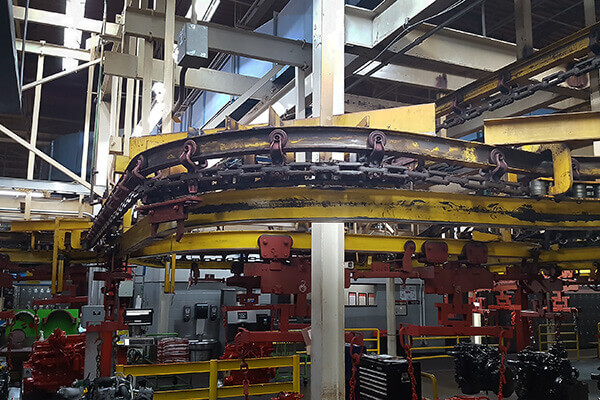
Power & Free Conveyors
Power & Free Conveyors are a dual-track overhead system that enables independent control of multiple carriers within a shared line. One track features a continuously moving powered chain. The second “free” track allows trolleys to stop, accumulate, transfer between lanes, or move at different speeds. As a result, power & free systems are highly adaptable for complex production environments.
These conveyors work well in operations that require load sequencing, buffering, or coordination with work cells, robots, or automation systems. The modular design supports branching, elevation changes, and variable pacing. This flexibility makes them ideal for high-mix, high-volume manufacturing or assembly lines with multiple work zones.
Best for: Complex layouts, accumulation, sequencing, and high-volume automation.
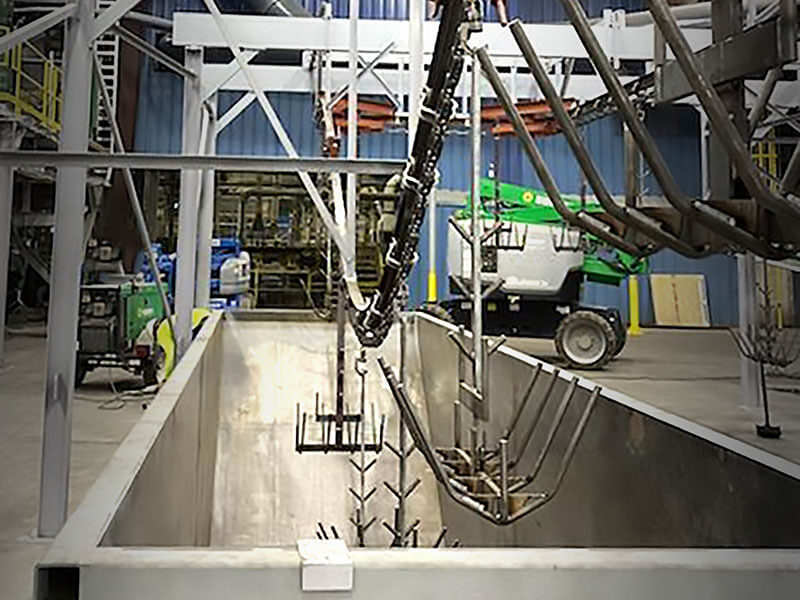
Specialty Overhead Systems
Specialty Systems are custom-engineered to meet unique environmental, spatial, or automation challenges. Many facilities use these conveyors in high-temperature zones, corrosive environments, cleanrooms, or operations that require advanced robotics and sensor integration.
To meet these needs, layouts, carriers, and structural components are fully customizable. Designs are based on your facility’s footprint, product handling needs, and process flow. You can tailor specialty overhead systems for unusual elevations, heavy loads, or integration with smart technologies and programmable controls.
Best for: Unique layouts, harsh environments, and automation-driven applications.
Applications & Uses
These systems are versatile and commonly used in the following production and movement settings:
Production & Assembly
-
Automotive and truck assembly lines
-
Engine, transmission, and drivetrain manufacturing
-
High-throughput multi-station operations
-
Work-in-progress transport between robotic cells or manual stations
Finishing, Storage & Movement
-
Finishing systems: painting, curing, drying, or coating lines
-
Part accumulation zones with stop/start capability
-
Overhead routing across facility zones or levels
-
Buffering between manufacturing and storage areas
-
Cross-floor or cross-department part delivery
Key Features
Engineered for performance and flexibility, overhead conveyors offer:
System Configuration
-
Overhead-mounted to free up valuable floor space
-
Available in 3″, 4″, and 6″ track sizes
-
Full Ball Open and Full Ball Sealed trolley options
-
Supports curves, inclines, switches, and turntables
-
Scalable, modular design for facility expansion
Functionality & Integration
-
In-house manufactured trolleys for Power & Free systems
-
Compatible with Monorail and Power & Free configurations
-
Stop/start functionality and accumulation zones
-
Integrates with PLCs, sensors, and robotics
-
Configurable for cleanrooms, high-heat, or corrosive environments
How Overhead Conveyor Systems are Engineered
It Starts with the Space
The layout defines the system. We map out your load and unload zones, workstations, clearances, and building structure. Overhead conveyors are ideal for weaving through tight spaces, around equipment, or above floor-level traffic — but only when planned with precision. Every path, elevation change, and support point gets factored in from the beginning.
The Load Shapes the Hardware
What you’re moving — its weight, size, and handling method — determines the trolley size, track size, and chain. Smaller loads may use X-348 chain and 3″ track. Heavier items may call for X-678 with 6″ track and sealed full-complement trolley wheels. As a result, even the attachments vary — from clevis pins and hooks to custom brackets and load bars.
Turns, Curves, and Transitions
Not all curves are the same. You’ll find both traction wheel and roller turns available in pre-engineered 30°, 45°, 60°, 90°, and 180° options. Engineers select each one based on space, speed, and load. For Example, vertical dips, inclines, and transitions get their own attention, too — because what goes up must be safely guided down.
Take-Ups, Drives, and Chain Pull
Whether manual, spring-loaded, or air-operated, take-up units keep the chain tensioned. Then the drive: Caterpillar or sprocket, chosen based on pull requirements and layout conditions. Behind the scenes, our engineers calculate chain pull, moving load, and lift forces to make sure every component — from drive size to curve radius — fits the system’s workload.
Hanging Methods and Safety Guards
How the conveyor hangs depends on your ceiling height, bay spacing, and structural steel. We design the supports to match your building, not force your building to fit our supports. And depending on your application, engineers add custom conveyor guards to protect workers and equipment alike.
For Power & Free Systems
We determine where loads should accumulate and how they’ll stop, switch, or sequence. Each switch is engineered based on flow, layout constraints, and carrier spacing to maintain throughput and minimize interruptions.
Downloads & Literature
Get in-depth specs, maintenance guides, and system planning resources
Ready to talk through your system?
Contact our team to start a conversation about your application, space, or load requirements.