Custom Engineered Conveyor Systems by Webb-Stiles
When Standard Conveyors Don’t fit, We Engineer the Solution
Custom engineered conveyor systems solve material handling challenges that off-the-shelf options can’t. That’s where Webb-Stiles comes in.
When standard conveyors fall short—whether due to product shapes, specialized processes, or space constraints—we design custom solutions built around your exact needs. These aren’t catalog items. They’re fully engineered conveyor systems created to fit your facility, your process, and your goals.
From concept to fabrication and installation, Webb-Stiles delivers systems that don’t just move products. We solve problems. When your project calls for something beyond the usual options, we’re ready to build the right solution.
How Webb-Stiles Approaches Custom Conveyor Projects
Every custom system starts with understanding your process.
At Webb-Stiles, we don’t force a product to fit your challenge. Instead, we follow a proven approach to engineer systems around your specific needs:
-
Process & Material Flow Analysis
We start by learning how your materials move. We identify constraints and pinpoint where standard conveyors fall short. -
Custom Engineering & Design
Our engineers design frames, fixtures, and automation components tailored to your operation. -
In-House Fabrication & Quality Control
Because we control manufacturing in-house, every system meets Webb-Stiles’ standards for durability and performance. -
Seamless Integration
Whether tying into existing lines or building new, we create solutions that work with your facility—not against it.
From concept to installation, Webb-Stiles leads the process to ensure your system is built right the first time.
Examples of Custom Engineered Conveyor Systems We’ve Built
Over the years, Webb-Stiles has engineered custom conveyor systems to solve unique challenges. Below are a few real-world examples of our work.
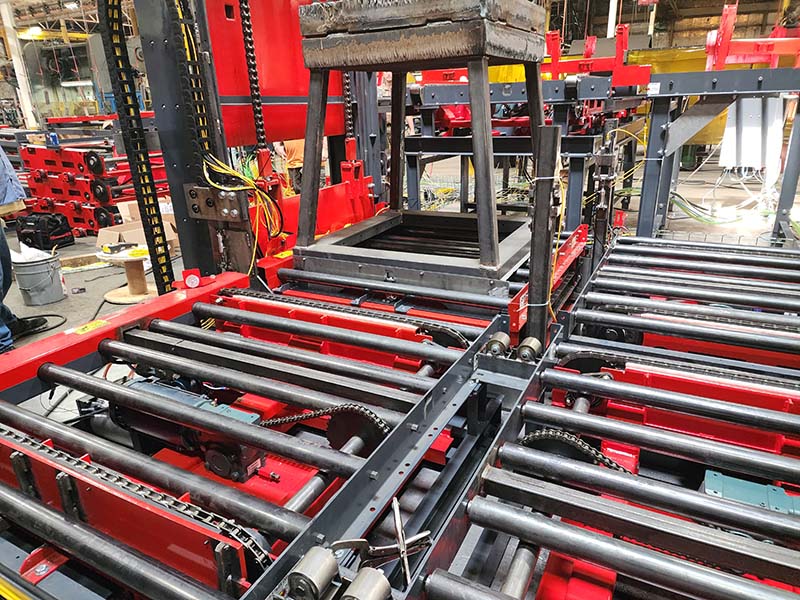
Custom Transport Conveyor System
Customer’s Challenge:
A large manufacturing facility needed to streamline how heavy transport hoppers moved through multiple process areas. These hoppers—up to 2100 kg each—had to travel through filling, weighing, inspection, and reject stations. Precise alignment and justification were critical at every stop. The system also required multi-level lifts, frequent directional changes, and seamless integration with customer-supplied controls. Plus, it needed to support phased installation with a modular layout.
Custom System Built:
Webb-Stiles engineered a transport system using chain-driven live rollers (CDLR), pneumatic pop-up stops, justification pushers, Serapid lifts, and weighing stations. Modular conveyors allowed phased start-up with air boards, chain transfers, and pushers. Webb-Stiles provided full mechanical, electrical, and pneumatic fabrication, installation, and debugging—while integrating with the customer’s control systems.
Problem Solved:
This custom system replaced manual handling with automated movement, designed for continuous 24/7 operation. It improved process flow, reduced operator strain, and ensured precise hopper positioning between workstations. The modular design offered flexibility for future expansion while maintaining high load capacity and precise control.
Why Custom vs. Standard Product:
Standard conveyors couldn’t meet the complexity of this project. Multi-directional transfers, precise alignment, and control system integration required a tailored solution. Webb-Stiles engineered a custom system with specialized lifts, pushers, and modular conveyors—built specifically for the plant’s workflow and operational demands.

Custom Vertical Plate Shot Blast Conveyor System
Customer’s Challenge:
A heavy plate fabricator needed a rugged system to safely move, tilt, and position steel plates—up to 60,000 lbs—for a vertical shot blast process. The equipment had to handle large plates with precise alignment, operate in tough blast shop conditions, and integrate smoothly with existing plant operations.
Custom System Built:
Webb-Stiles designed a conveyor system with two 50-foot tilt conveyors, a hydraulic pop-up transfer, and reinforced drive systems. Heavy-duty CDLR conveyors, hydraulic tilting bases, and custom plate positioners ensured safe, precise handling of large steel plates. Built for durability, the system was engineered for smooth, reliable performance in harsh environments.
Problem Solved:
This solution automated the plate handling process, reducing manual labor and improving safety. Tilt conveyors positioned plates accurately for blasting, while the hydraulic transfer conveyor ensured smooth, controlled movement between process stages.
Why Custom vs. Standard Product:
Standard conveyors couldn’t handle the size, weight, and rugged conditions of shot blast plate handling. Webb-Stiles engineered a custom system with specialized tilting, positioning, and transfer features—tailored to the customer’s specific needs and environment.
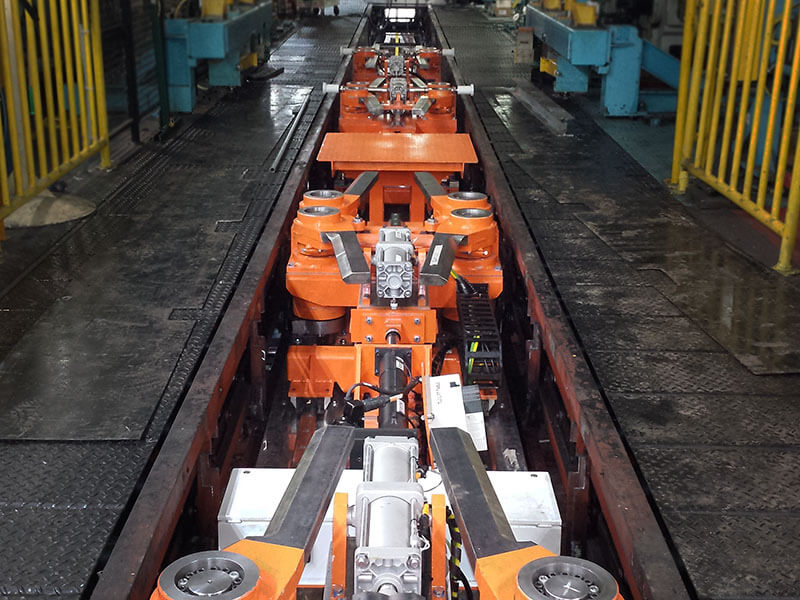
Custom Glass Body Shuttle Conveyor System
Customer’s Challenge:
A manufacturer needed a fully integrated assembly line to handle large, heavy refrigeration units. The system had to support assembly, tank build-up, and load testing, all while moving 900 lb upright freezers at high throughput. Existing equipment couldn’t meet the required cycle times, product flow, or ergonomic needs in a modernized assembly environment.
Custom System Built:
Webb-Stiles engineered and installed a complete conveyor system with motor-driven roller zones, Intralox belt conveyors, chain-driven live rollers (CDLR), pop-up transfers, upenders, destackers, scissor lifts, turntables, and tool rail structures. The system also included a tank build-up line and ULT carousel for continuous product flow. Custom controls, safety devices, and heavy-duty frames ensured reliable performance in high-demand production.
Problem Solved:
This solution automated material handling across the entire assembly process. It reduced manual labor, improved throughput to one unit every three minutes, and enhanced worker safety. The modular design allowed flexibility for future adjustments while supporting high-volume production.
Why Custom vs. Standard Product:
Standard conveyors couldn’t handle the project’s scale, product diversity, or process complexity. Webb-Stiles delivered a tailored system with engineered conveyor types, specialized lifts, and integrated operator stations. The result was a precise fit for the customer’s application and performance goals.
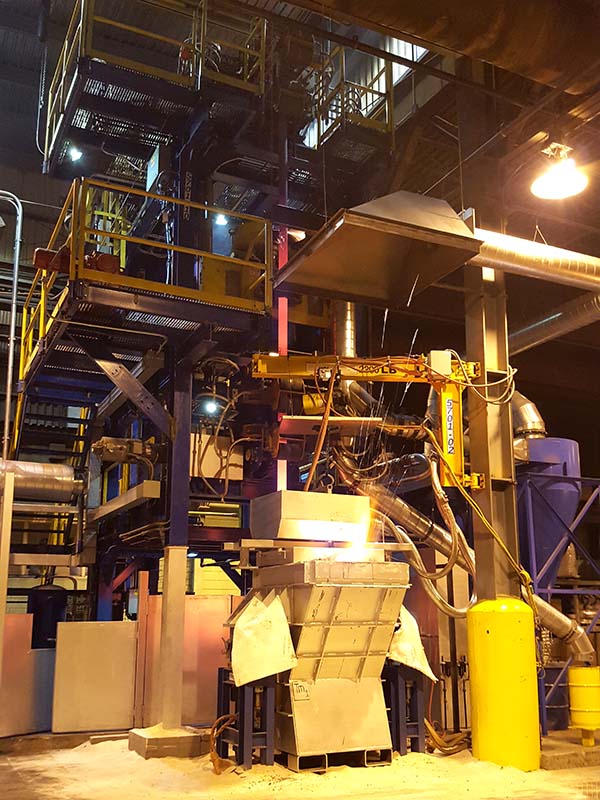
Custom Vertical Casting Tube Handling System
Customer’s Challenge:
An industrial casting facility required a fully integrated handling system to support its continuous cast tube operation. The system needed to accommodate tubes ranging from 3.25″ to 12.5″ in diameter and up to 99″ in length—moving them through a multistage process that included high temperatures, precise indexing, cutting, and downstream handling. Existing equipment couldn’t meet cycle time expectations or withstand the extreme foundry environment with 2000°F operating temperatures.
Custom System Built:
Webb-Stiles engineered and fabricated a complete material handling system centered around the vertical casting process. Key components included synchronized CAT drives, a programmable upender, integrated saw supports, automated tube transfer mechanisms, and a lowerator—all designed for hot and cold operational modes. The entire system was built to withstand foundry-grade thermal exposure and sustain up to 268 lbs per foot of product weight. Coordination included interface points for air, water, and hydraulic services, and the system was staged, tested, and validated at Webb-Stiles prior to installation.
Problem Solved:
The custom solution enabled precise, continuous tube handling without manual repositioning, meeting both thermal and mechanical requirements. Automated movement between stages reduced labor, increased safety, and maintained product integrity during each production cycle. The system successfully passed cold and hot runoff trials and was integrated into the customer’s casting line with minimal disruption.
Why Custom vs. Standard Product:
No standard system could withstand the load rating, temperature, or complex process flow required for this vertical casting application. Webb-Stiles designed a tailored solution around the facility’s exact needs, including molten metal handling considerations, precise synchronization between drive units, and high-strength components for continuous-duty operation.
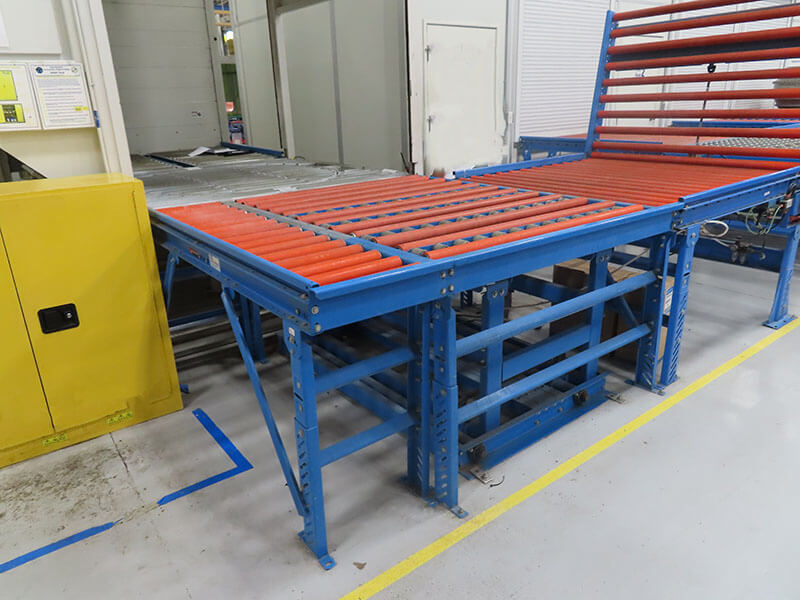
Custom Slave Pallet Handling Conveyor System
Customer’s Challenge:
A leading aerospace manufacturer needed to replace aging gravity conveyors with a powered system. This new system had to move a variety of heavy slave pallets through multiple process steps. These pallets, ranging from 24″ x 36″ up to 48″ diameter, needed to travel efficiently between workstations, dip tanks, and ovens—without manual repositioning. Frequent starts, stops, directional changes, and product variations made off-the-shelf conveyors impractical.
Custom System Built:
Webb-Stiles engineered a fully integrated chain-driven live roller (CDLR) system with pneumatic 90-degree pop-up transfers. The solution included powered conveyors with operator-controlled start/stop stations, specialized urethane-coated rollers, and reversible conveyors to interface with existing ovens and turntables. Every component was built for 24/7 operation, designed to handle 600 lb pallets with durability and precision.
Problem Solved:
The new system automated pallet transfers, reducing manual handling and operator strain. It improved product flow, increased efficiency, and integrated smoothly with existing equipment. At the same time, it maintained Webb-Stiles’ high standards for durability and uptime.
Why Custom vs. Standard Product:
Standard conveyor packages couldn’t meet this project’s demands. Frequent 90-degree transfers, dip tank integration, and unique pallet sizes required a custom approach. Webb-Stiles designed and built a tailored system to match the facility’s layout, product specs, and operational needs.
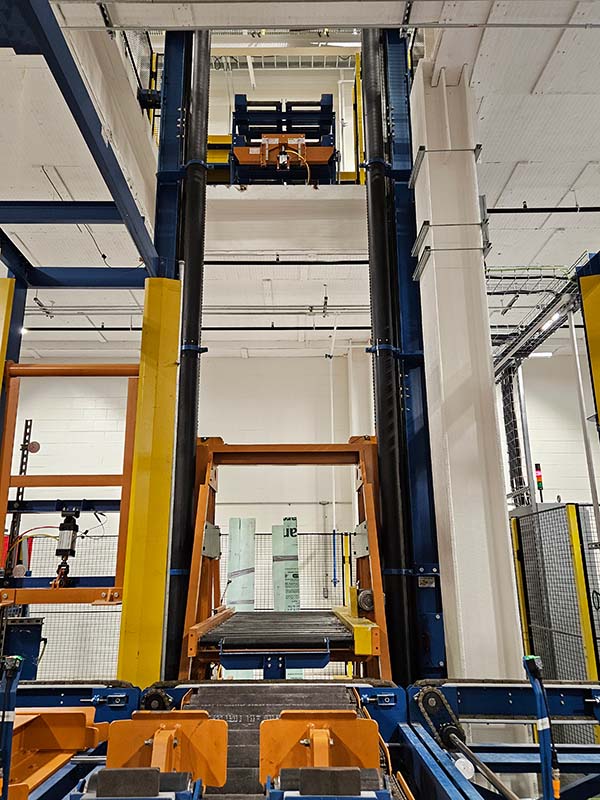
Custom Rod & Pallet Handling System
Customer’s Challenge:
A manufacturer needed to automate a complex material handling process involving heavy pallets and delicate rods. The system had to de-stack pallets, remove support boards, elevate them for manual unpacking, and return components for re-stacking. All of this had to meet strict cleanliness and safety standards.
Custom System Built:
Webb-Stiles engineered a fully integrated rod and pallet handling system. It included pallet de-stackers, vertical lifts (VRCs), singulators, custom de-palletizers, and chain-driven live roller conveyors (CDLR). This system automated both vertical and horizontal movement of heavy loads across two floors while protecting sensitive materials.
Problem Solved:
The solution eliminated manual lifting and repositioning of heavy pallets and boards. It reduced damage to delicate products and improved efficiency by automating repetitive, labor-intensive tasks.
Why Custom vs. Standard Product:
Off-the-shelf conveyors couldn’t meet the demands of this project. Heavy loads, multi-level product flow, and contamination-sensitive materials required a custom approach. Webb-Stiles designed a system with specialized lifts, Serapid chain actuators, and precision conveyors to fit the application’s exact needs.
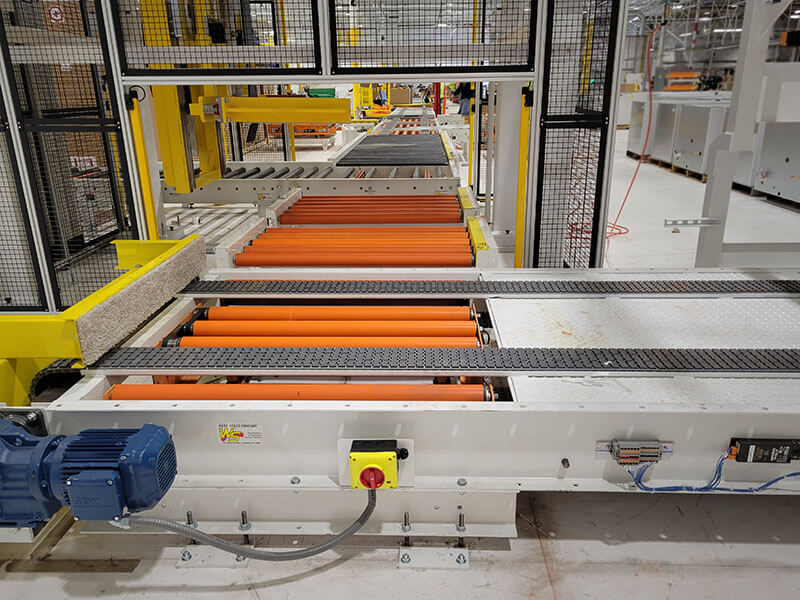
Custom Assembly Line Conveyor System
Customer’s Challenge:
A major manufacturer needed to replace a 25-year-old shuttle system used to transfer vehicle bodies from an assembly slat conveyor to glass installation stations. The new system had to handle multiple vehicle models, maintain tight positioning tolerances, and integrate smoothly with existing processes. At the same time, it needed to improve reliability and cycle times.
Custom System Built:
Webb-Stiles engineered a turnkey glass body shuttle system with dual super-duty scissors lifts, servo-driven slide tables, tire grabbers, tire pushers, and precision shuttle mechanisms. The system included advanced positioning systems, high-cycle ball screw actuators, and a new controls package with Mitsubishi PLCs and HMIs. Heavy-duty shuttle frames, hardened tracks, and rugged components were designed for continuous use in demanding production environments.
Problem Solved:
This custom solution automated the precise lifting, positioning, and transferring of vehicle bodies for glass installation. It improved accuracy and reduced cycle times while cutting maintenance downtime. The new system maintained compatibility with existing equipment, ensuring a smooth upgrade from outdated machinery.
Why Custom vs. Standard Product:
Standard conveyor systems couldn’t meet the demands of high load capacity, precision positioning, and integration with existing slat conveyors and camera systems. Webb-Stiles delivered a fully engineered solution tailored to the application’s performance, durability, and operational needs.
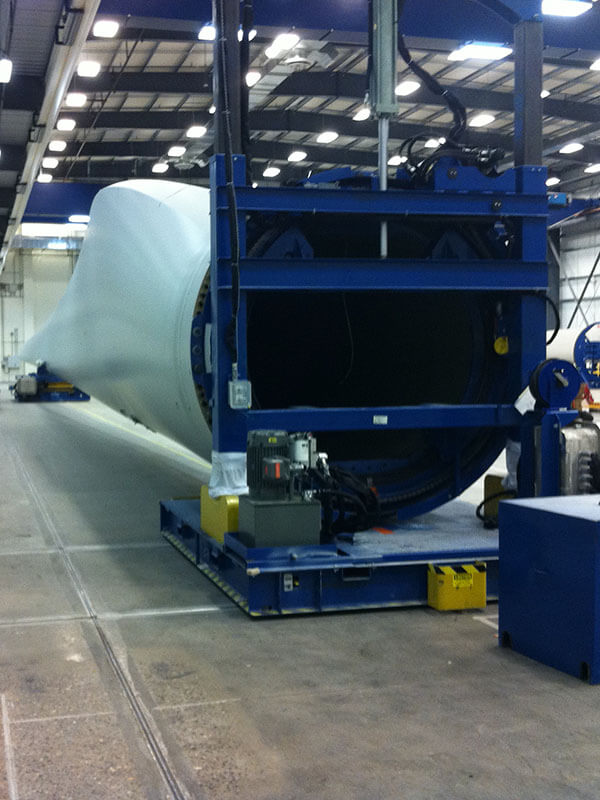
Custom Towline System w/Rotators & Tipping Stations
Customer’s Challenge:
A manufacturer of large composite components needed a floor-mounted towline system to transport and manipulate oversized molds through a multi-stage process. The system had to accommodate variable load sizes, allow 180° rotation, and incorporate both manual and automated tipping stations—while remaining fully accessible for operators across multiple work cells.
Custom System Built:
Webb-Stiles designed and fabricated a heavy-duty recessed towline system paired with custom-engineered carts and handling equipment. The complete solution included motorized rotation devices, manual and automated tipping mechanisms, and a hand-push cart to support flexible movement outside the powered line. Each element was tailored to fit the customer’s layout, load geometry, and process flow. Carts were built with tracking rollers, tow arms, and lift points for safe transport. The system was staged, tested, and documented prior to shipment to ensure smooth on-site integration.
Problem Solved:
This integrated solution allowed large, irregular parts to be safely transported, rotated, and tipped at key workstations without manual lifting or repositioning. The dual approach of manual and automated tip stations provided flexibility for both high- and low-volume areas, while the rotate devices ensured efficient orientation for downstream processing.
Why Custom vs. Standard Product:
Due to the complexity of handling large composite structures and the need for flexible material flow, no off-the-shelf tow system could accommodate the tipping, rotating, and transport requirements in a single layout. Webb-Stiles’ custom carts and powered devices enabled seamless process integration, while meeting safety, ergonomic, and throughput goals.
Ready to solve your material handling challenge? Contact Webb-Stiles today.
See custom conveyor systems in action—follow Webb-Stiles for real project builds, shop floor highlights, and engineering solutions.