Conveyor Rollers
Whether you’re moving light packages or powering heavy-duty loads, conveyor rollers are the foundation of efficient material handling. From gravity-fed lines to motor-driven live roller systems, Webb-Stiles offers a full range of rollers engineered for performance, durability, and seamless integration.
Additionally, all rollers are manufactured in-house using our automated roll machine, ensuring consistent quality and total customization flexibility. Standard options are available in a wide range of diameters, gauges, and bearing types. For unique needs, custom configurations are built to meet the most demanding application requirements.
Looking for a specialty or oversized roller? Nevertheless, we build those in-house too—and every roller is proudly made in the USA.
Jump to:
Types of Conveyor Rollers
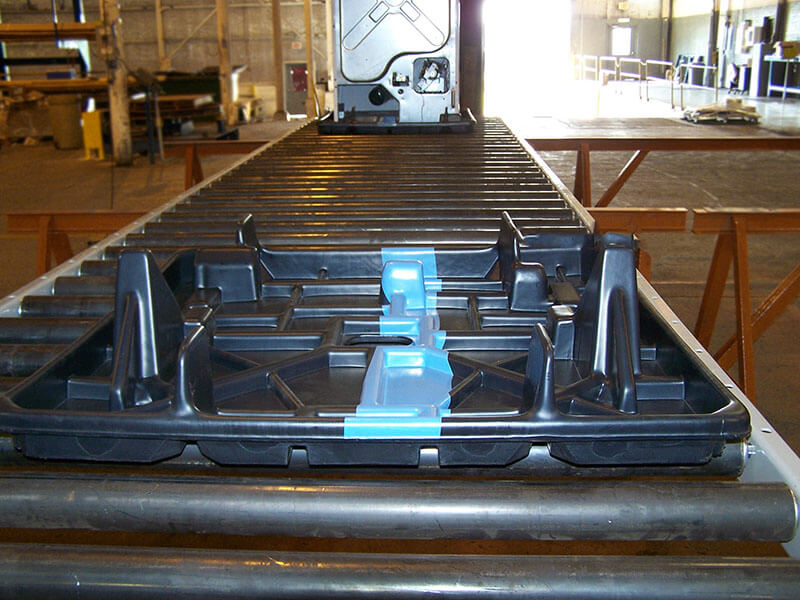
Gravity Rollers
Design & Operation:
Gravity rollers use a slight incline to move products without power. Each roller spins freely on bearings, as a result, items coast across the surface using natural force. Additionally, shafts are spring-loaded for quick replacement.
Key Benefits:
- Low cost, low maintenance
- Quiet and energy-free operation
- Simple to install and reconfigure
Applications:
Manual pick lines
Packaging and fulfillment
Warehouse transfer sections
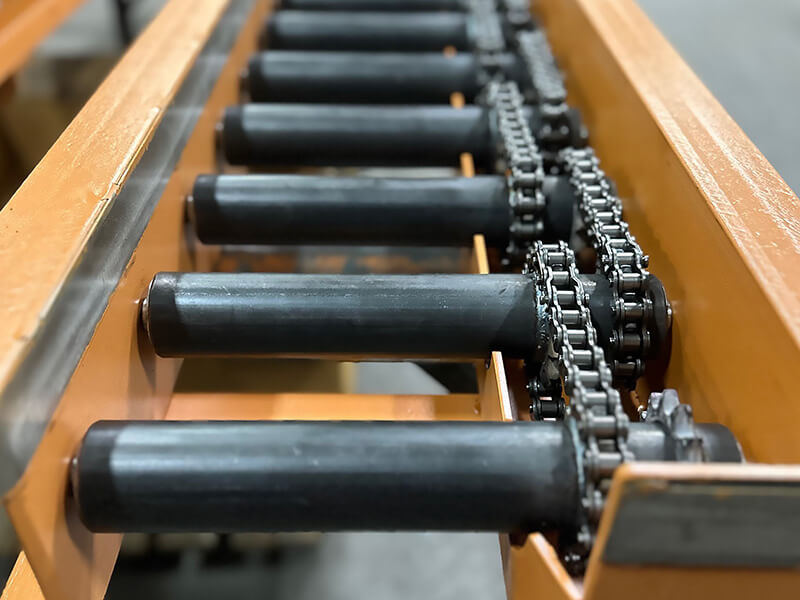
Sprocketed Rollers
Design & Operation:
Sprocketed rollers use fixed-position sprockets that engage with drive chains, ensuring consistent, positive movement. Consequently, they’re ideal for heavy loads, indexing, or powered transfer systems. Multiple sprockets and shaft styles are available.
Key Benefits:
High torque and load capacity
Reliable movement without slippage
Durable in harsh or dusty environments
Applications:
Chain Driven Live Roller (CDLR) systems
Vertical or robotic conveyors
Stop-start indexing or accumulation
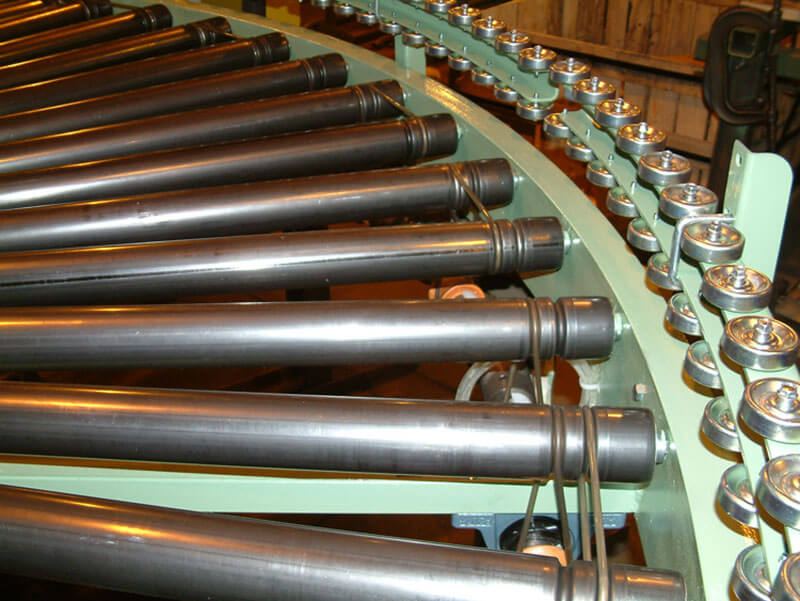
Lineshaft Rollers
Design & Operation:
Lineshaft rollers are powered by a single shaft running beneath the conveyor. In addition, elastic bands drive individual rollers, enabling accumulation and gentle product handling. In short, they’re ideal for light to medium loads.
Key Benefits:
Safe and quiet operation
Low energy consumption
Accumulates without sensors or controls
Applications:
Order fulfillment
Manufacturing workstations
Distribution centers
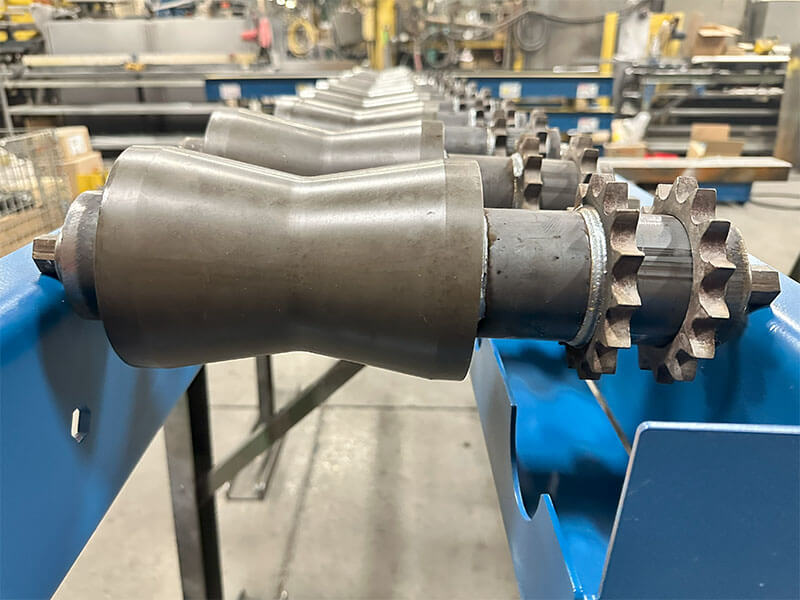
Specialty Overhead Systems
Design & Operation:
Built in-house to your exact specifications using our automated roll machine. Specialty rollers include tapered, impact, grooved, oversized, bowtie, and motorized options—all precision-fit for your system layout and function. As a result, they support both standard and complex overhead designs.
Key Benefits:
Designed for unique loads or layouts
Engineered for integration with new or existing systems
Compatible with Webb-Stiles and competitor equipment
Applications:
Curved or vertical conveyors
Harsh load zones or robotic cells
Heavy-duty manufacturing and custom automation
Examples of Specialty Rollers
Custom 5″ Roller with Snap Ring Grooves
Welded in-house with precision grooves to retain bearings under high load conditions.
Vertical Sprocketed Roller for Robotic Application
Custom-built for vertical operation in a robotic painting carousel system.
CDLR Roller with Round Shaft and Welded Sprockets
Heavy-duty CDLR roller with a round shaft and welded sprockets for fixed drive engagement.
Key Features of Webb-Stiles Conveyor Rollers
Built to meet the demands of real-world material handling, our conveyor rollers combine strength, precision, and versatility. In short, from standard models to custom-engineered designs, every roller is manufactured in-house for consistent performance throughout your entire system.
Heavy-Duty Construction
All rollers are built from heavy wall steel tubing, with ends reamed or swaged in-house for precision bearing fits. Standard models range from 1″ to 3.5″ in diameter and support loads up to 5,850 lbs. As a result, they’re well-suited for demanding applications. For example, many of our rollers are used in rugged environments like heavy equipment transfer lines.
Precision-Machined Shafts
Standard hex shafts are spring-loaded for easy tool-free installation. Optional round shafts and snap ring grooves are available for specialized applications. In addition, these options improve fit and alignment. That way, installations stay fast and consistent even in tight timelines.
Wide Bearing Selection
Choose from free-running, grease-packed, semi-precision, or precision bearings—each selected based on your speed, load, and environmental requirements. Ultimately, this flexibility ensures optimal performance in any setting. For example, free-running bearings are often chosen for light package handling, while precision bearings serve high-torque zones.
Urethane Sleeve Option
Increase grip and protect delicate products with urethane-coated rollers, available in multiple colors and friction ratings. Because of this, they’re ideal for sensitive handling zones. Even so, they remain compatible with most standard roller designs.
Noise-Reducing Hushveyor Option
Our exclusive Hushveyor rollers dampen high-frequency noise and reduce overall sound levels by up to 10 dB—without altering system layout or roller performance. As such, they support both safety and comfort.
Made In-House, Made in the USA
All standard and specialty rollers are manufactured at Webb-Stiles facilities using our automated roll machine for tight tolerances and consistent quality. That means every unit is built under the same process controls, no matter the size or configuration. What’s more, you don’t have to worry about third-party lead times or off-site delays.
Bearings Explained
The performance of a conveyor roller depends heavily on the bearing inside. Webb-Stiles offers a complete range of bearing styles to meet the needs of different systems—from manual push lines to high-torque, motorized conveyors.
Free-Running Bearings
Designed for low-resistance rotation, these bearings are ideal for gravity conveyors. They require no lubrication and allow products to move smoothly with minimal push force. Because of this, they’re a reliable choice for quiet, low-maintenance systems.
Best For:
Gravity-fed lines
Low-maintenance systems
Quiet, efficient movement
Grease-Packed Bearings
Sealed and lubricated for life, these bearings offer long-lasting performance under higher loads and speeds. As a result, they’re the standard in most live roller and chain-driven conveyors.
Best For:
CDLR and LSLR systems
Belt-driven applications
Dirty or high-moisture environments
Precision & Semi-Precision Bearings
For demanding or specialty applications, precision and semi-precision bearings offer tighter tolerances, higher load ratings, and smoother operation. In these cases, performance and control are critical.
Best For:
High-speed or high-load conveyors
Powered accumulation zones
Custom or robotic integration
Need help choosing the right bearing? Our team can help specify the best option based on your speed, load, and operating environment.
Hushveyor Technology
Workplace noise isn’t just an annoyance — it’s a safety and productivity concern. That’s why Webb-Stiles developed Hushveyor, a roller innovation that reduces noise without requiring changes to your system layout or operation.
How It Works
Hushveyor rollers are engineered with internal damping features that absorb impact and vibration during both start-up and continuous rolling. Unlike other noise-reducing options, they don’t require any changes to your layout or drive configuration.
Test Results
Independent acoustic testing showed significant reductions in overall sound pressure:
Up to 5 dB quieter during impact events
Up to 10 dB quieter during continuous rolling
High-frequency resonances (like 4500–9000 Hz) virtually eliminated
Altogether, that translates to a 2–3x reduction in perceived noise to the human ear. Additionally, results show noise pressure levels drop by up to 10 dB across both impact and rolling conditions.
Key Benefits
Helps meet OSHA noise level standards
Improves operator comfort and safety
No impact on conveyor speed, torque, or performance
Available on multiple roller types and sizes
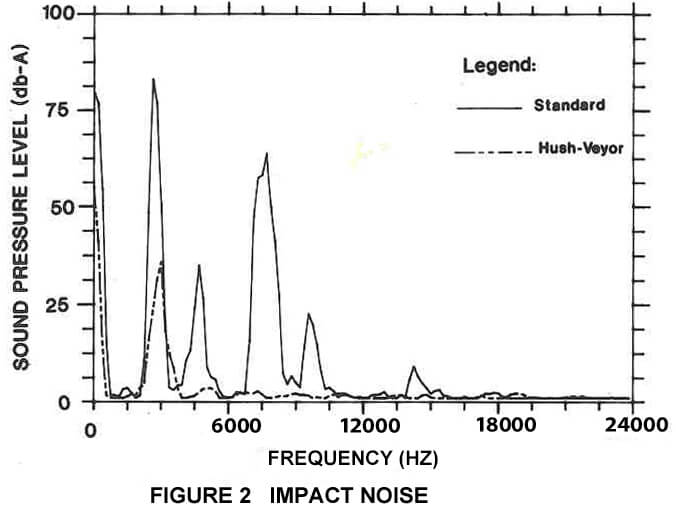
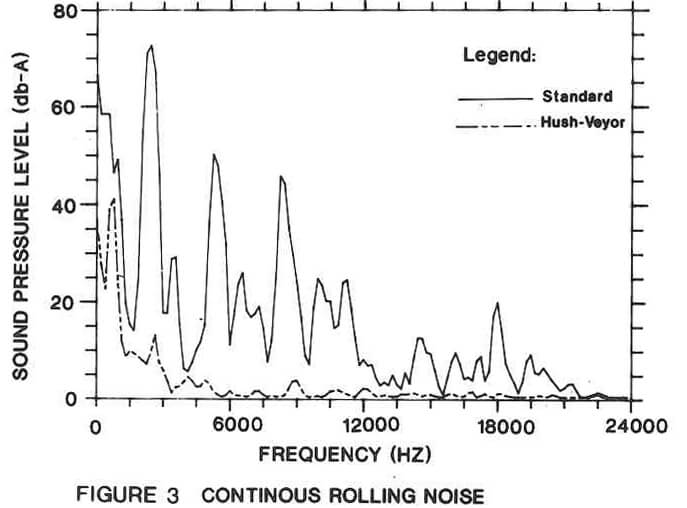
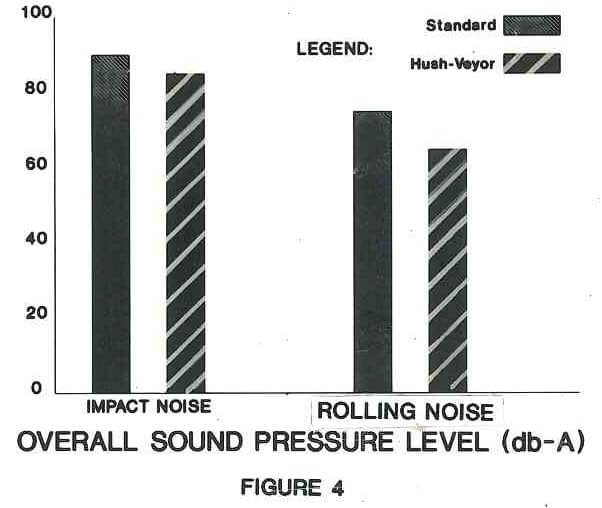
In-House Manufacturing
At Webb-Stiles, every conveyor roller is built in our own facility using a custom-engineered automated roll machine. Because of this we are able to maintain complete control over quality, lead times, and custom capabilities—without relying on outside suppliers.
Precision at Every Step
From tubing prep and cutting to reaming, swaging, and final assembly, every stage is performed by our skilled team. In each phase, shafts, bearings, and custom features are installed in-house, with rigorous checks at each step.
Flexible for Any System
Whether you’re ordering 10 standard rollers or 1,000 custom builds, our process is designed for fast turnarounds and consistent output. As a result, we produce all standard roller sizes and can fabricate up to:
96” BF for swaged rollers
104” BF for reamed rollers
A full range of shaft styles, bearings, and sprocket configurations
Standard Conveyor Roller Sizes
Whether you’re designing a new system or replacing existing rollers, our standard sizes offer a reliable starting point for most applications. These rollers are produced in-house for consistent performance, fast turnaround, and seamless integration with a wide range of conveyor layouts.
Need a custom size? We can engineer it. Nevertheless, these standard sizes are available for fast delivery.
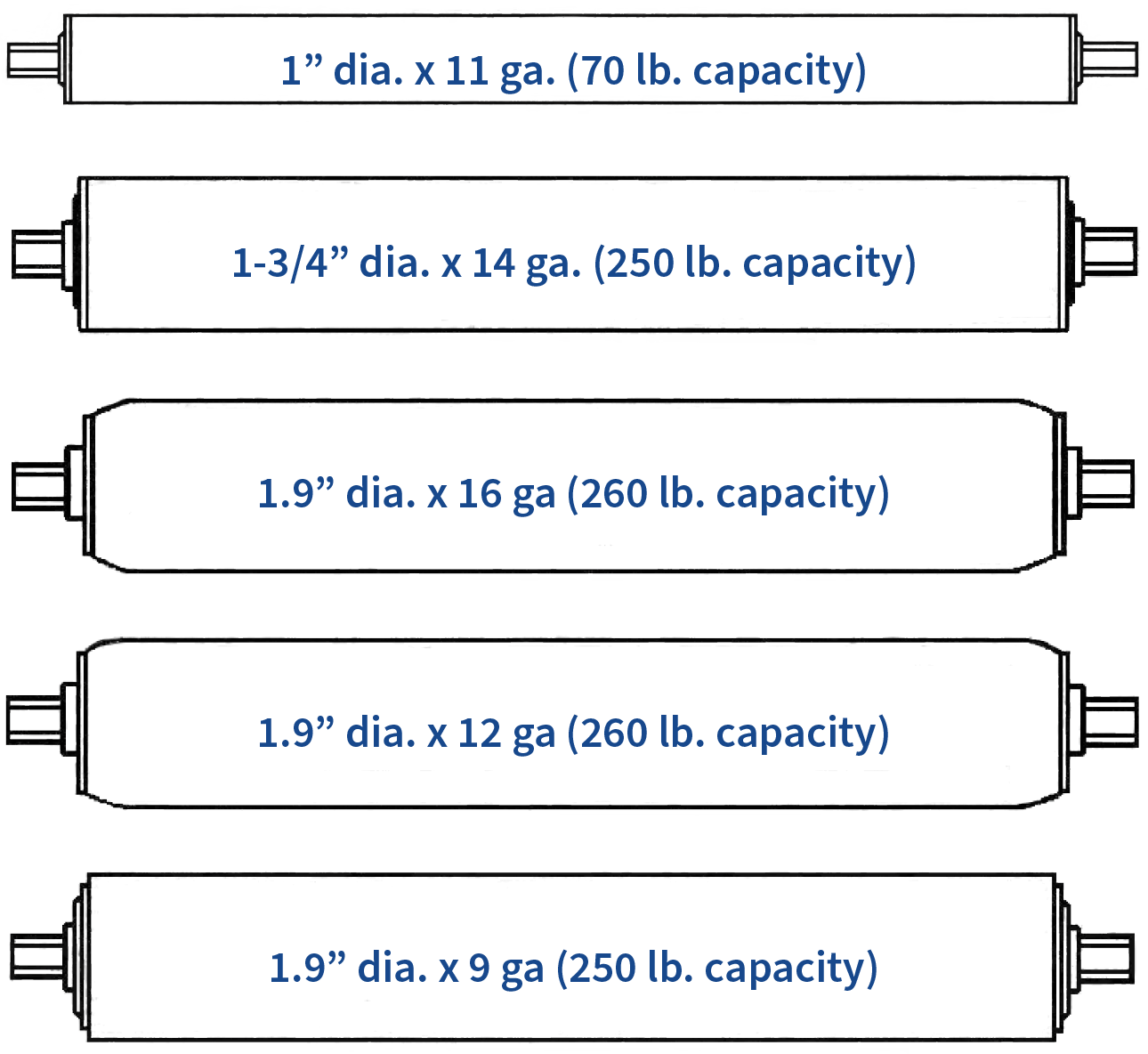
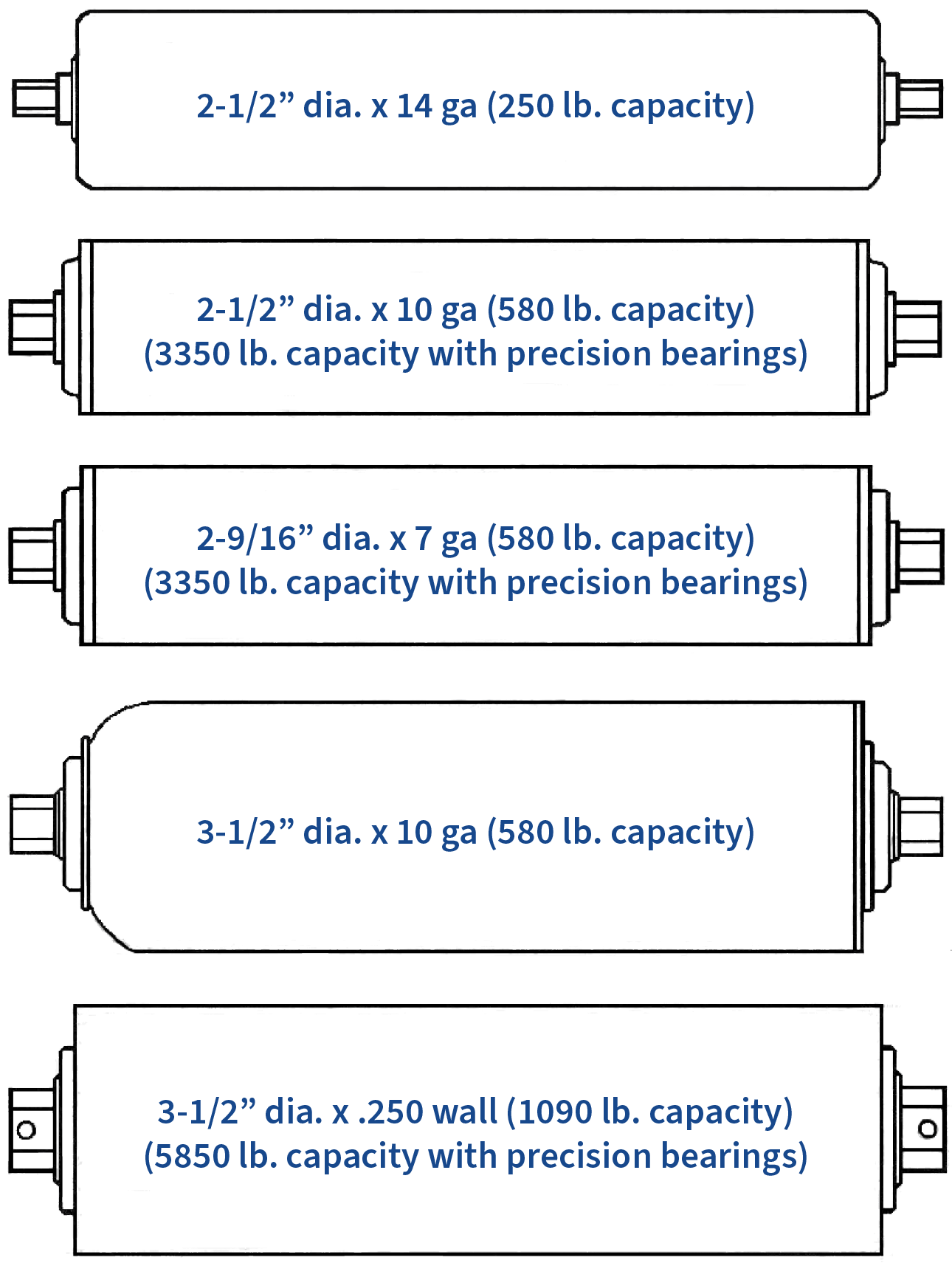
How To Order Conveyor Rollers
Webb-Stiles rollers are available as part of complete conveyor systems or as individual units—whether you’re an OEM building your own line or need replacements for existing equipment. To help you get started, here’s what we’ll need based on your situation:

Included in a New System
If you’re purchasing a complete conveyor system from Webb-Stiles, we’ll select the correct rollers during the engineering process.
What We Determine:
Roller type based on layout (gravity, lineshaft, CDLR, etc.)
Load weight, spacing, and material requirements
Shaft style and bearing fit
Drive needs (sprockets, grooves, friction surface)
As a result, no additional action is needed—we’ll spec everything in-house and include it in your project proposal.
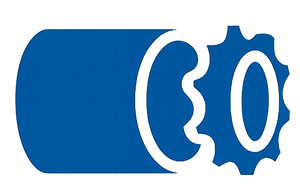
Stand-Alone Rollers (OEM, Retrofit, or Replacement)
If you’re ordering rollers outside of a full Webb-Stiles system—whether for your own build or to replace existing units—we’ll need a few specs to get started.
What to Provide (if known):
Between Frame (BF) dimension
Roller diameter & wall gauge
Shaft style (hex, round, keyed, etc.)
Bearing type (free-running, grease-packed, precision)
Drive features (sprockets, grooves, urethane sleeve)
Quantity and any special details
Don’t worry if you’re missing some of this information—send what you can, and we’ll help figure out the rest.
Roller Measurements and Required Specs
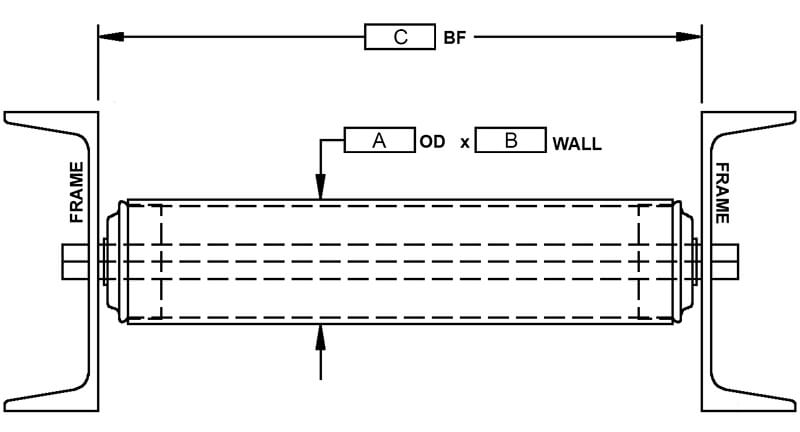
Gravity Roller
A. Outer (Roller) Diameter
B. Wall Thickness (Gauge)
C. Between Frame Width (BF)
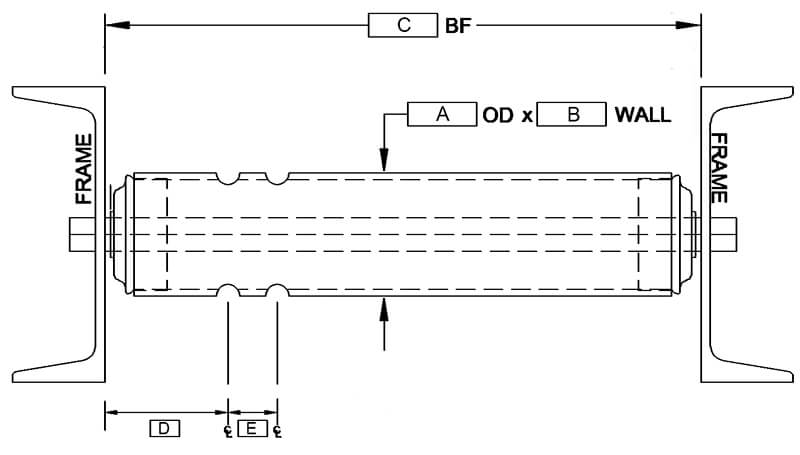
Grooved (Lineshaft) Roller
A. Outer (Roller) Diameter
B. Wall Thickness (Gauge)
C. Between Frame Width (BF)
D. Groove Locations
E. Distance between Grooves
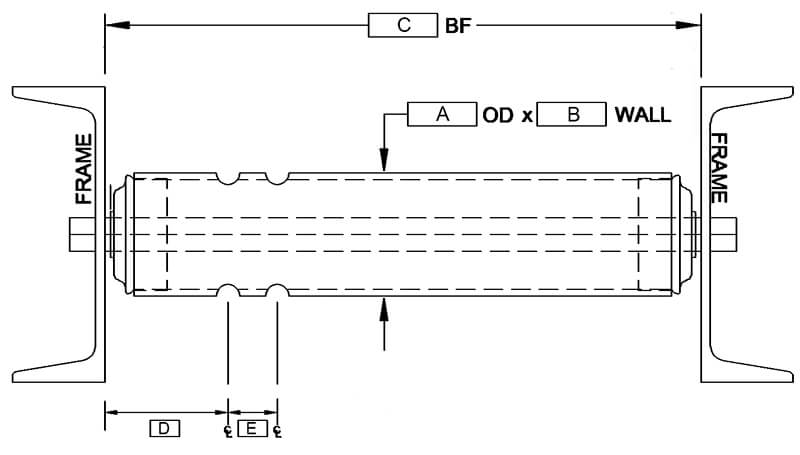
Sprocketed Roller
A. Outer (Roller) Diameter
B. Wall Thickness (Gauge)
C. Between Frame Width (BF)
D. Sprocket Locations
E. Distance between Sprockets
1. Download the Roller Order Guide
Includes part number format, shaft/bearing options, and configuration tips. Additionally, if you want a step by step reference, refer to pages 16 – 18 of the brochure.
2. Complete the Roller Quotation Request Form
Need help? Send us a message and we’ll walk through it together
Still Have Questions?
Our team knows roller specs inside and out. If you’re unsure about what to submit, just send what you do know — we’ll help you figure out the rest.